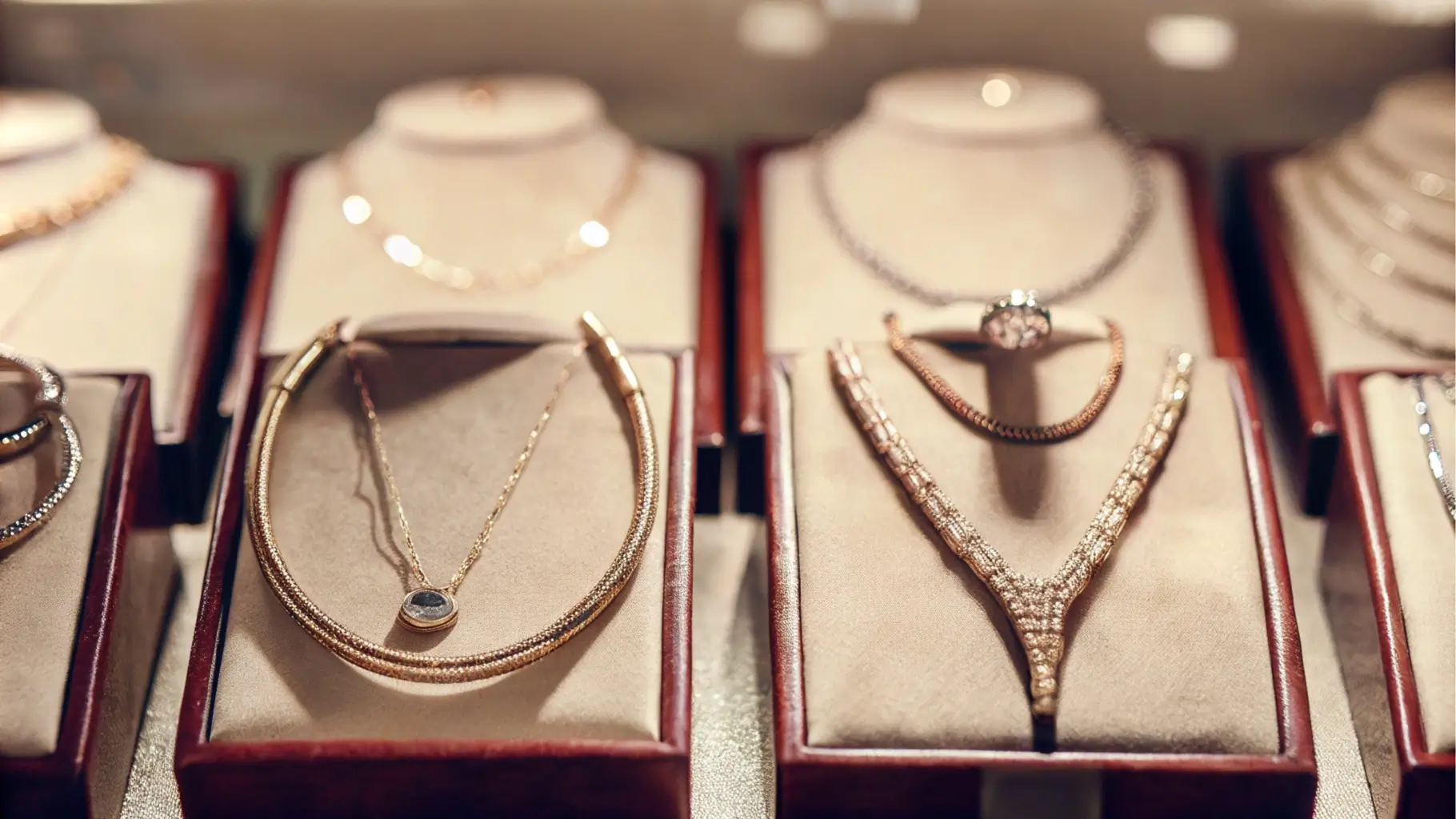
How Custom Boxes Elevate Napier Jewelry’s Value
2024-12-13
For many jewelry brands, jewelry boxes go beyond the meaning of containers, and serve as a carrier of jewelry brand stories and a bond of emotional connection with consumers. Richpack is a China jewelry box manufacturer with nearly 20 years of experience in jewelry packaging, and also provides exclusive custom jewelry box manufacturers USA. In Richline factory under Richpack, from high-end luxury jewelry gift boxes to simple and exquisite cosmetic packaging, every detail contains our pursuit of quality and respect for craftsmanship, and every link is strictly controlled. Next, let us explore in depth, understand all the art and skills behind jewelry box printing and packaging in one article, and analyze this professional field that combines aesthetics and technology in all aspects.
From the initial flash of design inspiration to the birth of the final exquisite product, every link in the production of Richpack paper jewelry boxes is a careful arrangement of materials, craftsmanship and ingenuity. In the following content, we will analyze layer by layer, explore each stage, uncover the secrets and techniques, and see how the raw materials are transformed into stunning packaging that can set off the charm of jewelry.
When determining the design of paper jewelry box, first of all, we should deeply analyze the characteristics of the jewelry, including the shape, size, weight, texture and style of the jewelry. For the irregular shape of the jewelry, such as shaped gemstones, need to design a special inner support structure to ensure its stability in the box; for the larger weight of the jewelry, paper boxes need to focus on the structural strength and load-bearing capacity, to avoid damage due to the inability to withstand the weight in the transportation or storage process. At the same time, we should fully communicate with customers to understand their brand positioning, target audience and market demand. If the brand positioning for high-end luxury, then the paper boxes design should focus on reflecting the sense of dignity and sophistication, can adopt a simple atmospheric design style, with high-grade printing technology and special materials; if the target audience is young consumers, the design can be integrated into the fashion, personalized elements, such as popular color combinations and unique pattern modeling, in order to attract the attention of the young groups. In addition, the practicality and convenience of paper boxes should also be considered, such as whether they are convenient to open and easy to carry. By combining these factors, using professional design software to design, draw the plan of paper boxes and three-dimensional rendering, to ensure that the design not only meets the basic function of protecting jewelry, but also to show the brand characteristics, attracting the attention of consumers.
The main green materials for paper jewelry box production include paper and gray board. Paper, common white cardboard, coated paper, specialty paper and so on. White cardboard firm and thick, quantitatively larger, front whiteness and high gloss, paper surface smoothness and delicate, with good printing suitability, suitable for the printing effect of the higher requirements of the surface of the paper boxes, can be clearly rendered printed patterns and text, showing a simple and generous texture; coated paper surface smooth, high color reproduction, printing patterns of bright colors, rich layers, often used in the production of Need to show exquisite patterns and delicate colors of the jewelry box, such as inlaid with colored stones jewelry box packaging; special paper has a unique texture, texture or special properties, such as pearlescent paper can show a pearlescent effect, increase the sense of magnificence of the paper boxes, often used in the production of high-end jewelry boxes, to enhance the grade of the product.
Gray board is mainly used to enhance the structural strength of paper boxes, common single gray, double gray, all gray and other types. Single gray board is gray on one side, the other side is relatively smooth, the price is more economical, suitable for the appearance of the requirements are not particularly high, but need to support a certain strength of the paper boxes; double gray board both sides are gray, uniform texture, high strength, commonly used in the production of ordinary grade jewelry boxes; full gray board is in the strength and stability of the performance of the more outstanding, suitable for the structural strength of the requirements of the high quality of large-scale jewelry boxes or high-grade jewelry gift boxes. box or high-grade jewelry gift box. When choosing materials, it is necessary to make a comprehensive consideration according to the design requirements of jewelry boxes, cost budget and environmental protection standards, etc., to ensure that the selected materials can not only meet the quality requirements of the products, but also comply with the environmental protection trend of the market and the enterprise’s cost control objectives.
When the materials such as paper and gray board arrive, a strict incoming material inspection should be carried out immediately. Richpack factory quality management personnel will first carefully check the quantity of materials and count them one by one according to the delivery list to ensure that the arrival quantity is consistent with the order to avoid omissions that affect subsequent production progress.
For paper, the first test quantitative, using a professional quantitative balance to measure accurately, to ensure that its grammage in line with the procurement standards, the deviation is controlled within a very small range, because the quantitative directly affects the stiffness and thickness of the paper, which in turn affects the effect of paper boxes molding. Whiteness and gloss are measured with the help of a whiteness meter and a gloss meter to ensure that their values correspond to the standards of the selected paper type. The smoothness of the paper surface is detected by a smoothness meter. Poor smoothness can lead to uneven ink adhesion and affect the clarity of the print. For the FSC-certified gray board, the focus of the test thickness uniformity, using micrometers in different positions multi-point measurement, to ensure that the thickness error does not exceed the prescribed range, the thickness of uneven paper boxes will make the structure of uneven stress, reducing the strength. At the same time, the compressive strength testing equipment to detect the compressive strength of the gray board, to ensure that it can meet the jewelry box in different use scenarios.
Common printing methods are offset printing, flexographic printing, gravure printing, etc., which have their own applications in paper jewelry box printing. Offset printing is one of the more widely used printing methods, which is characterized by high printing accuracy, can clearly restore the details of the pattern and text, for the printing of delicate lines, exquisite patterns and high-quality color images have obvious advantages, suitable for the production of high-end paper jewelry boxes with high requirements on printing quality. For example, when printing paper boxes with delicate jewelry patterns or delicate brand logos, offset printing can accurately render the colors and textures of the patterns, making the printing effect realistic and vivid. Flexo printing has unique advantages for specific applications. Flexo printing uses water-based ink, which is environmentally friendly and non-polluting, in line with the current consumer demand for environmentally friendly products. At the same time, the printing pressure of flexo is small, suitable for printing all kinds of texture of paper, including some thinner or softer paper, for the need to print large color blocks or simple patterns on paper boxes, flexo can quickly and efficiently complete the printing, and the cost is relatively low, suitable for the production of low and medium-end paper jewelry box.
Gravure printing printing ink layer is thick and solid. The printing ink layer of gravure printing is thick, the color is bright, saturation is high, the printing quality is stable, suitable for printing needs to show a strong visual effect and high texture of the paper jewelry box, such as some high-end luxury jewelry box, through the gravure printing can show the jewelry of the sparkle of the light and luxury texture. However, gravure printing has higher plate cost and longer printing cycle, so when choosing the printing method, you need to consider the factors such as the positioning of the jewelry box, the printing quantity, the cost budget, and the requirement of the printing quality, in order to determine the most suitable printing method.
In paper jewelry box printing, color management is crucial, which directly affects the consistency of the printing effect with the packaging design draft and the visual appeal of the product. First of all, we should establish a perfect color management system and use professional color measurement equipment, such as spectrophotometers, to calibrate and match the color of the electronic files before printing. In the printing process, strictly control the temperature and humidity of the printing environment, because these environmental factors will have an impact on the paper’s stretch and the ink’s drying speed, which will lead to color deviation. At the same time, it is necessary to ensure that the ink volume of the printing machine is controlled accurately, and the printing machine is regularly maintained and debugged to ensure that the ink supply from the ink hopper of each printing unit is uniform and stable.
For pattern printing, it is necessary to select the appropriate printing process and printing plate according to the requirements of the design. In the production of printing plates, to ensure the clarity and accuracy of the graphics, to avoid problems such as lost dots, deformation and so on. In the printing process, attention should be paid to the overprinting accuracy of the pattern, by adjusting the parameters of the printing machine and the positioning device, to ensure that the pattern of each color is accurately overprinted, to avoid ghosting, misalignment and other phenomena. In addition, you can also use some special printing processes, such as spot-color printing, hot stamping, UV printing, etc., to enhance the visual effect and three-dimensional sense of the pattern, so that the paper jewelry box is more beautiful, unique, highlighting the value of jewelry products and brand image.
Varnishing and laminating is the common process of paper jewelry box surface finishing, they have an important impact on the appearance and protective properties of paper boxes. Varnish process is a layer of varnish coated on the surface of the printed materials, so that after drying to form a layer of colorless transparent film. According to the type of varnish and coating method is different, can be divided into glossy varnish, matte varnish and partial UV varnish and so on. Bright varnish can make the surface of paper boxes show high gloss, enhance the colorfulness and visual impact of the printing pattern, make the jewelry box look more bright and exquisite, suitable for the pursuit of gorgeous effect of jewelry box packaging; matte varnish gives paper boxes a low-key, elegant texture, reduce light reflection, make the surface of the paper boxes softer and more delicate, for some people who pursue simplicity and elegance.
The matte varnish gives paper boxes a low-profile and elegant texture, reduces light reflection, and makes the surface of paper boxes softer and more delicate. For some jewelry brands pursuing simple and high-end style, the matte varnish paper boxes can better reflect their brand temperament; local UV varnish is to carry out varnish treatment in specific patterns or areas, to highlight the key patterns or words on the paper boxes through the contrast between the local and other matte or common surfaces with high gloss and to add a sense of hierarchy and three-dimensional sense. Laminating process is the plastic film through the adhesive laminating on the surface of the printed materials, forming a paper-plastic integrated finished product.
Common types of lamination are glossy film and matte film. The surface of the paper boxes after lamination is as bright as a mirror, the color is more bright and colorful, with good waterproof, moisture-proof, wear-resistant performance, can effectively protect the printed pattern, prolong the service life of the paper boxes, applicable to the appearance of the brightness and protection performance requirements of the jewelry box; lamination of the matte film of the paper boxes presents a soft, elegant matte effect, comfortable to the touch, but also has a certain degree of three-dimensionality of the finished product. The matte film coated paper boxes present a soft and elegant matte effect, which is comfortable to the touch, and also has certain waterproof and wear-resistant performance, which is often used in the pursuit of texture and unique style of high-end jewelry box packaging. When choosing the varnishing and laminating process, it is necessary to take into account the design style of the jewelry box, the cost budget and the requirements for the protection performance and other factors, in order to achieve the best finishing effect.
In the laminating process, the laminator plays a key role. The common laminating machine is mainly composed of unwinding device, gluing device, hot pressing device, winding device and other parts. Its working principle is: first of all, the unwinding device will be rolled plastic film and printed paper boxes paper were unfolded; then, the gluing device in the plastic film surface evenly coated with a layer of adhesive, adhesive role is to make the film and paper can be firmly combined together; subsequently, after the coating of film and paper into the hot press device, at a certain temperature and pressure, the adhesive is activated, the film and paper tightly affixed. Subsequently, the coated film and paper enter the hot pressing device, and under certain temperature and pressure, the adhesive is activated, and the film and paper are tightly adhered to each other; finally, the adhered finished product is wound up by the winding device. In this way, the perfect combination of plastic film and printed materials is realized, and the comprehensive performance of paper jewelry box is enhanced. When choosing the varnishing and laminating process, it is necessary to comprehensively consider the design style of the jewelry box, the cost budget, and the requirements for the protection performance and other factors, in order to achieve the best finishing effect.
Special processes such as hot stamping and embossing can significantly enhance the aesthetics and texture of paper jewelry boxes. Hot stamping is to transfer metal foil or pigment foil to the surface of paper boxes by hot pressing, forming patterns or characters with metallic luster or special colors. Common hot stamping materials include gold foil, silver foil, laser foil and so on.
In the hot stamping operation, it is divided into automatic hot stamping machine and manual hot stamping machine two ways.
Manual hot stamping machine needs to manually place the paper boxes under the hot stamping plate, after adjusting the position, manually operate the handle to press down, so that the hot stamping plate and the paper boxes contact, through the heating and pressure, the hot stamping foil will be transferred to the surface of the paper boxes in the specified position.
The process of this method is relatively simple, but the efficiency is low and the proficiency of the operator is required to be high. Its function is mainly applicable to small batch, personalized customized jewelry box hot stamping needs, such as some niche high-end jewelry brands launch limited edition products, manual hot stamping machine can accurately meet its unique pattern hot stamping requirements. The significance of the existence of manual hot stamping machine is that it is highly flexible, low cost of equipment, for the initial attempt to hot stamping process or unstable order volume of small jewelry box production enterprise, is a more economical choice.
The automatic hot stamping machine realizes the automatic production process, the paper boxes are automatically transported to the hot stamping station by the conveyor, the sensor accurately locates the position of the paper boxes, the hot stamping plate is automatically pressed down and contacted with the paper boxes under the instruction of the control system, after completing the hot stamping operation, the paper boxes are then transported to the next process. The automatic hot stamping machine is powerful, with high speed and high precision hot stamping ability, it can realize continuous production, which greatly improves the production efficiency, and the quality of hot stamping is stable, and the position of the pattern is highly accurate. It is of great significance to the mass production of jewelry box production enterprises, can meet the market demand for a large number of jewelry boxes, reduce the unit cost of production, and at the same time to ensure the consistency of the stamping effect of the product, enhance the overall image of the brand.
Hot stamping process can make the jewelry box present a gorgeous, noble temperament, the gold luster can be echoed with the bright light of the jewelry, to enhance the product grade, commonly used in high-end jewelry brand packaging; hot stamping silver process gives a simple, stylish feeling, suitable for some of the pursuit of modern style of the jewelry box; laser hot stamping to produce a unique laser effect, such as rainbow-like radiance and changing patterns, increase the visual appeal of the paper boxes and anti-counterfeiting. Laser hot stamping can produce unique laser effect, such as rainbow light and changing patterns, increasing the visual attraction and anti-counterfeiting performance of paper boxes, commonly used in some innovative and personalized jewelry box design.
Pressure embossing process is to use pressure to make the surface of paper boxes form a raised or depressed pattern, through the three-dimensional effect to enhance the layered sense of paper boxes and texture. For some jewelry patterns with three-dimensional sense, such as flowers, animal shapes, etc., the embossing process can make them more vivid and realistic, as if leaping out from the surface of the paper boxes, bringing consumers a strong visual impact and tactile experience. In addition, hot stamping and embossing process can be combined to create a richer and more diverse effects, further enhance the uniqueness and artistic value of the paper jewelry box, so that it stands out among the many packages and attracts the attention and love of consumers.
From ordinary to amazing, what secrets are hidden behind the gorgeous transformation of packaging? You can also read this article to further explore the infinite possibilities of hot stamping, embossing and other special processes, and the answer lies there.
Die cutting is the process of cutting the printed paper according to the designed shape and size, and its accuracy plays a decisive role in the molding quality of paper boxes. In the die-cutting process, first of all, to ensure the precision of the production of die-cutting knife plate, die-cutting knife plate design should be completely consistent with the planar expansion of paper boxes, knife plate lines should be smooth, accurate, to avoid burrs, deviations and other problems. At the same time, to choose a reliable quality of die-cutting tool, the sharpness and durability of the tool directly affects the effect and efficiency of die-cutting. In the die-cutting operation, to strictly control the die-cutting pressure and speed, too much pressure may lead to paper rupture, deformation, pressure is too small will make the die-cutting is not complete; speed is too fast may affect the die-cutting accuracy, speed is too slow will reduce production efficiency. In addition, there is a need for regular maintenance and repair of die-cutting equipment, check the transmission components of the equipment, positioning devices and other normal operation, to ensure the stability and accuracy of the equipment. In the die-cutting process, we should pay attention to the positioning and fixing of paper to prevent paper displacement in the die-cutting process, affecting the die-cutting accuracy. Through strict control of these die-cutting process points, to ensure that the edges of the die-cut paper boxes neat, accurate size, for the subsequent assembly and use to provide a good foundation.
Gray board grooving is to make the paper boxes can form accurate angle and shape when bending, grooving angle, depth and other parameters have an important impact on the bending effect of paper boxes. Generally speaking, the common slotting angles are 90 degrees and 120 degrees, etc. 90 degrees of slotting is suitable for making paper boxes with right-angle bends, such as common square jewelry boxes; 120 degrees of slotting is commonly used to make paper boxes with certain oblique angles, so as to make paper boxes more unique in appearance. The depth of the groove should be determined according to the thickness of the gray board, generally the depth of the groove is controlled between one-third and one-half of the thickness of the gray board is more appropriate. If the grooving depth is too shallow, paper boxes may appear in the bending crease is not clear, bending difficult situation, affecting the molding effect of paper boxes; if the grooving depth is too deep, the strength of the gray board will be weakened, resulting in the use of paper boxes easy to rupture, affecting its structural stability. In the process of grooving, professional grooving equipment should be used, and ensure the precision and stability of the equipment. At the same time, we should check the quality of the gray board after grooving to see whether the angle and depth of the groove meet the requirements, whether the groove wall is smooth, with or without burrs and other issues. Only by guaranteeing the quality of the grooving of the gray board can the paper boxes be bent accurately after assembly to form a regular shape and meet the structural and appearance requirements of the jewelry box.
Laminating is the process of pasting the printed surface paper and gray board together by glue, and its operation process and glue selection are crucial. Before laminating, it is necessary to pre-treat the gray board and printed face paper to ensure that the surface is clean, flat, and free of dust, oil and other impurities, so as to ensure that the glue can give full play to the bonding effect. Then, according to the paper boxes material and design requirements to choose the right glue, common glue has white latex, hot melt adhesive and so on. White latex adhesive has the advantages of high adhesive strength, moderate drying speed, environmental protection, etc., suitable for most of the paper material laminating; hot melt adhesive has a fast curing speed, adhesive strength, commonly used in the need for rapid molding of the laminating process. In the laminating process, to control the amount of glue coated, coated too much will lead to glue overflow, affecting the appearance of paper boxes, may also cause uneven adhesion between the surface paper and gray board; coated too little will lead to adhesion is not strong, paper boxes are prone to gluing phenomenon. Generally, roller coating and spraying can be used to apply glue to ensure that the glue is evenly distributed on the surface of the gray board or the paper. Next, accurately fit the face paper on the gray board, using pressing equipment or hand tools for pressing, so that the face paper and gray board tightly combined, to exclude the middle of the air bubbles. After laminating is completed, the laminating paper boxes should be placed in a well-ventilated environment with suitable temperature for drying, avoiding drying in humid or high temperature environment, so as not to affect the curing effect of the glue and the quality of the paper boxes.
Assembly of paper boxes is the process of combining the laminating parts into complete paper boxes, in this process, it is necessary to ensure that the structure of paper boxes is stable and the appearance is neat. First of all, we should accurately position and align the components of the paper boxes according to the design requirements to ensure that the folding lines and interface positions are accurate. For some paper boxes with special structure, such as sky and earth cover boxes, book-type boxes, etc., attention should be paid to the precision of coordination between various components, such as sky and earth cover boxes, the size of the lid and the box body should be matched to ensure that the lid can be tightly covered in the box, and open and close smoothly; book-type boxes, the outer shell and the inner box of the pasting position should be accurate, so that the inner box can be securely fixed in the shell, and the appearance of a smooth.
During the assembly process, some auxiliary tools, such as jigs and positioning molds, can be used to help fix the parts and ensure the accuracy and stability of the assembly. For the parts that need to be pasted, the appropriate amount of glue should be applied again to ensure that the paste is firm. At the same time, attention should be paid to the location and amount of glue to avoid glue contamination of the surface of the paper boxes, affecting the appearance. After the assembly is completed, the paper boxes should be inspected as a whole to see whether the structure of the paper boxes is solid, whether the connection between the various components is tight, and whether the appearance is flat, no wrinkles, no deformation, etc. If there is any problem, adjustments should be made in time. If there are any problems, adjustments and repairs should be made in time to ensure that the final assembled paper boxes meet the quality standards and can provide good packaging protection for jewelry.
In the assembly of paper boxes, the automatic packaging machine plays a key role in greatly improving the production efficiency of jewelry packaging manufacture and product quality. Its operation process mainly includes the following key links.
Firstly, the paper is delivered automatically, through the photoelectric sensor and counter to identify and count the feeding port, and then with the help of traction system and slider, the paper will be automatically sent to the next process, to ensure the accuracy and stability of the paper delivery. Next is the vacuuming and suction link, which utilizes the airflow system to suck the paper and carry out the dust removal process to ensure that the surface of the paper is clean and dust-free, providing a good foundation for the subsequent processing. This is followed by loading and laminating. The laminating machine automatically attaches the adhesive edge to the edge of the paper to ensure the tension and overall fastness of the paper. In the embossing and folding section, the embosser embosses the paper, and the folding machine then folds the paper to form the basic framework of the box appearance. Finally, the box body molding and the installation of heaven and earth cover, the bottom positioning cam and side positioner will fold the cardboard smooth molding, complete the molding of the box body, and then use the pneumatic pressure suction cups to fix the box body on the rotary table, through the glue plate spray glue will be installed in the box body at both ends of the heaven and earth cardboard, complete the heaven and earth cover all the molding of the paper boxes.
Richpack’s fully automated paper boxes production line integrates a variety of advanced automation equipment and technology, with the automatic box wrapping machine as the core, realizing the whole process of automation operation from paper feeding, laminating, assembling to finished product output. The production line adopts advanced PLC program control system, which is able to automatically monitor various indexes and parameters during the whole production process, and control and adjust the human-machine interface to ensure the accuracy and stability of the production process. At the same time, advanced servo motors and servo controllers are used to realize precise control and adjustment of various mechanical parts in the production process to ensure the high efficiency and reliability of the equipment operation. In addition, the Richpack line is equipped with a high-precision transmission system that utilizes gear reducers and timing belt drive technology to achieve efficient and stable transmission and rotation of various mechanical components.
· Paper feeding: the core of this process is accurate paper positioning and efficient transportation. Using Fidelity paper feeding system, using vacuum adsorption and mechanical drive combination, the paper in the pile of paper sheet by sheet separation and transported to the main drive track. Through the precision adjustment of the front gauge and side gauge, the gripper size is strictly controlled to ensure that when the paper enters the subsequent process, the lateral and longitudinal positioning error is controlled within ±0.1mm, which ensures the high precision and stability of paper conveying. For example, in the face of different weights and materials of paper, Fidelity paper feeding system can automatically adjust the adsorption force and feeding speed to adapt to the characteristics of the paper.
·Gluing: High-precision gluing equipment is selected. According to the characteristics of the paper and the glue, the gluing amount is precisely regulated. Methods such as roller coating or spraying are adopted to ensure that the glue is evenly coated on the paper surface. During the gluing process, the flow and pressure of the glue are monitored in real – time to ensure the stability of gluing. Meanwhile, the gluing thickness is strictly controlled, generally within an appropriate range, to ensure a good bonding effect and avoid problems caused by excessive or insufficient glue, laying a solid foundation for subsequent assembly and other processes.
·Assembling: Multi-axis linkage robot and intelligent positioning tooling are adopted to work together. According to the preset program, the robot grabs the laminating parts, and under the guidance of high-precision visual recognition system, the parts are accurately placed in the positioning tooling. The servomotor-driven robot arm realizes the alignment, pressing and sticking operations of the parts. For paper boxes, high-precision molds are used to ensure that the size matching accuracy of the lid and the box body is within ±0.2mm, guaranteeing smooth opening and closing; when assembling the book-type boxes, an intelligent positioning system ensures that the deviation between the inner box and the outer shell pasting position is controlled within a very small range, guaranteeing the appearance of a smooth and beautiful.
·Finished product output: After the assembly of paper boxes is completed, the automatic inspection line carries out all-round quality inspection. Using laser scanning, image recognition and other technologies, the paper boxes are quickly inspected for dimensional accuracy, appearance defects, structural strength and so on. Qualified paper boxes are sorted and packaged according to specifications and batches through the automatic sorting and packaging system, realizing efficient output and storage management of finished products. If paper boxes are found to have dimensional deviations or appearance defects during the inspection process, the system automatically sorts them into the defective area for subsequent rework.
Overall, in the production process, the production line has a very high degree of automation, which can realize the automated control and management of the whole production process, significantly improve production efficiency and reduce production costs. And stable operation, low noise, good environmental protection, will not produce greater pollution and harm to the environment and employees. At the same time, its safe and reliable characteristics, can realize the whole production process of automated detection and protection, effectively avoid accidents in the production process, for the mass production of high-quality paper jewelry box provides a strong guarantee.
Quality is the life of a factory box brand. A tiny flaw in a jewelry box may affect the display effect of the jewelry and even damage the reputation of a high-end jewelry brand. Therefore, during the quality inspection stage, we have formed a professional and rigorous quality inspection team, using high-precision measuring tools to measure the size of the jewelry packaging box in detail to ensure that the length, width, height and dimensional errors of each folding part are strictly controlled within a very small range. At the same time, with rich experience and keen observation, we carefully check the clarity of the printed pattern, color accuracy, overprint accuracy, and the perfection of the surface finishing process, without missing any details. Below, we will show you the importance of this link from the aspects of strict quality inspection standards and careful packaging design.
Quality inspection is the key to ensure the quality of the paper jewelry box, and needs to be carried out in strict accordance with the standards and methods. Richpack factory Richline is equipped with professional and responsible quality inspection staff, who, with their rich experience and professional knowledge, carry out meticulous control of every step of the production process.
In terms of dimensional inspection, the QC staff use appropriate precision measuring tools, such as calipers, straightedge, etc., to measure the length, width, height and folded parts of the paper boxes to ensure that the deviation from the designed dimensions is within the permissible range, and that the deviation of the dimensions in general should be controlled to be within ±0.5mm, so as to ensure that the paper boxes can be perfectly adapted to the jewelries and will not be affected by dimensional problems during the transportation and storage process. In order to ensure that the paper boxes can fit perfectly with the jewelry, and will not affect the use during transportation and storage due to the size problem.
Printing quality inspection is mainly through the combination of visual inspection and professional equipment testing, to check the clarity of the printing pattern, color accuracy, overprinting accuracy and so on. Patterns should be clear, without blurring or ghosting, and the color should be consistent with the design without obvious color difference; overprinting accuracy requires that the overprinting error of the main pattern should not exceed ±0.1mm, and that of the secondary pattern should not exceed ±0.2mm; for paper boxes with barcodes, the quality inspectors will use a barcode tester to check the clarity and scanability of the barcodes to ensure that the barcodes can be accurately identified.
Richpack has a specialized compression testing workshop, equipped with professional compression testing instruments. During the structural strength test, we simulate the actual use of paper boxes, such as compression test and drop test, to check whether the paper boxes will be deformed or ruptured when they are subjected to certain pressure and impact. Compression test requires paper boxes to keep their shape intact without obvious deformation under the pressure of a certain weight; drop test requires paper boxes to fall freely from a certain height without damage to the internal structure and appearance, and be able to continue to protect the jewelry.
Surface flatness and cleanliness are also important aspects of quality inspection. The quality inspectors will carefully check whether the surface of the paper boxes is flat, and whether there are any defects affecting the appearance such as wrinkles, bumps or depressions. At the same time, ensure that the surface of paper boxes is free of dust, stains, fingerprints and other contaminants to ensure the neatness of the product. For special craft effects such as hot stamping and embossing on paper boxes, check whether they are clear, complete and free from problems such as peeling and blurring.
In addition, the quality inspection staff will also check the surface finishing effect of the paper boxes, such as whether the stamping is firm, whether the varnishing or laminating is even, and whether there are bubbles, wrinkles and other defects. Through comprehensive and strict quality inspection, it is ensured that only qualified products enter the next stage.
Environmental protection testing is also crucial, which is related to consumer health and environmental safety. Richpack has a specialized environmental protection testing workshop and advanced testing instruments to carry out comprehensive environmental protection performance testing of paper boxes, of which formaldehyde testing is one of the key testing items. The formaldehyde test is one of the key testing items. We use professional formaldehyde detectors to accurately test the formaldehyde release of paper boxes in accordance with strict testing procedures. According to the relevant national and industry standards, we ensure that the formaldehyde emission of paper boxes is far below the stipulated safety threshold, ensuring that the products are green and environmentally friendly, and will not cause any health hazards to consumers.
For example, the 3V-EDX6600ROHS detector equipped in the factory was developed to meet the requirements of ROHS, halogen-free, and the toy directive, and has many advanced features. It uses a US-type Si-pin detector, is electrically cooled rather than liquid nitrogen cooled, is compact, provides accurate data analysis and is low-maintenance.
The SES signal enhancement processing system developed by the company can effectively improve measurement sensitivity. The instrument can measure 75 elements from sulfur (S) to uranium (U), with an elemental content analysis range of 2ppm-99.99%. The measurement time can be adjusted between 100-300s, and it can automatically switch between seven light path correction collimation systems according to different samples, achieving one-button automatic testing. It is easy to operate and has a friendly interface. This instrument can accurately detect the content of heavy metals such as lead (Pb), mercury (Hg), cadmium (Cd), hexavalent chromium (Cr6+) and other hazardous substances such as polychlorinated biphenyls (PCBs) and polybrominated diphenyl ethers (PBDEs) that may be contained in paper boxes, ensuring that the product complies with the requirements of relevant regulations and standards such as the ROHS Directive, the US CPSIA Act and China’s GB standards.
In addition, in order to detect volatile organic compounds in paper boxes, Richpack factory Richline uses a professional gas chromatography mass spectrometer (GCMS). It can accurately analyze and quantitatively detect volatile organic compounds such as aldehydes, benzenes, and toluenes that may be present in paper boxes. This instrument can accurately measure the content of these volatile organic compounds to determine whether paper boxes pose a potential threat to human health and the environment.
For the detection of plasticizers, the Richline factory uses advanced testing equipment to strictly test the content of plasticizers (such as phthalates) to ensure that it is within a safe range. Through these comprehensive and professional environmental protection tests, the Richpack factory line is committed to providing consumers with green, environmentally friendly and safe paper jewelry box products, fulfilling its corporate social responsibility and promoting the sustainable development of the industry.
Paper jewelry boxes that have passed quality inspection need to be packaged and stored appropriately. In terms of packaging methods, it is common to use batch packaging, in which a certain number of paper boxes are neatly stacked, wrapped with plastic film or wrapping paper, and then placed in a cardboard box. Cushioning materials such as foam boards and bubble bags should be placed inside the cardboard box to prevent the paper boxes from being damaged during transportation due to collisions and extrusion. The surface of the carton should be clearly marked with information such as the product name, specifications, quantity, production date, and manufacturer to facilitate identification and management. For storage, the packaged paper boxes should be stored in a dry, ventilated, and cool warehouse to avoid direct sunlight and humid environments. The temperature in the warehouse should be controlled between 15℃-25℃, and the relative humidity between 40%-60%. Such environmental conditions can effectively prevent paper boxes from becoming damp and deformed, moldy and deteriorated, and the printed patterns from fading. At the same time, regular inspections should be carried out on the stored paper boxes to check for any quality issues. If problems are found, they should be dealt with promptly to ensure the quality stability of the products in stock, so that qualified paper jewelry boxes can be provided in a timely manner when needed.
The production process of plastic hinged jewelry boxes is not a simple manufacturing process, but a wonderful performance that combines cutting-edge technology, ingenious ideas and ultimate craftsmanship. From the idea when receiving the order, to the selection of high-quality materials, to the use of advanced injection molding technology, every step is refined. In the following content, let us explore the production process of plastic hinged jewelry boxes in depth.
After receiving customer orders for plastic hinge jewelry boxes, sales staff must communicate in depth and detail with the customer. The salesperson needs to understand the customer’s specific requirements for the plastic hinge jewelry box, including precise measurements such as length, width, height, and thickness, as well as the shape of the box, such as square, round, or irregular, to ensure that the subsequent production can meet the customer’s actual needs. For jewelry boxes, the internal dimensions need to accurately fit all types of jewelry to avoid instability or inability to fit due to dimensional deviations.
In design phase, the Richpack team discusses the appearance of the plastic box with the customer, clarifying specific requirements for elements such as color, pattern, and text, as well as whether special design elements, such as brand logos and anti-counterfeiting marks, need to be incorporated. The customer’s specific needs for the structure of the plastic box are understood, such as whether functional structures such as compartments, drawers, and flaps need to be designed to better display and protect the jewelry products. At the same time, the company’s production capacity, craftsmanship, and the types of materials available are explained in detail to provide the customer with professional advice and references to help them optimize the design plan, making it more feasible and cost-effective to produce while meeting aesthetic and functional requirements. Through sufficient communication, we ensure that both parties agree on the design and production requirements of the jewelry box, laying a solid foundation for subsequent proofing and production.
Based on the requirements determined through communication with the customer, the design department uses professional design software such as Adobe Illustrator and CorelDRAW to design and draw the box, creating a two-dimensional plan view and a three-dimensional rendering to visually display the appearance and structure of the box. During the design process, full consideration is given to the feasibility of the production process to ensure that the design can be successfully transformed into a practical product. After the design is complete, the design files are transferred to the sampling workshop, where the sampling personnel select the appropriate raw materials for sampling and production based on the design requirements. During the sampling process, Richpack employees strictly control the process parameters of each link, such as injection molding temperature, pressure, time, etc., to ensure the quality and accuracy of the sampling products. After the sampling is complete, a comprehensive quality inspection of the samples is carried out, including an appearance inspection to check whether the surface is smooth, whether there are any defects, and whether the color meets the requirements; a dimensional measurement to use high-precision measuring tools to check whether the dimensions of the samples are consistent with the design dimensions; and a structural test to check whether the plastic box opens and closes smoothly and whether the various parts are firmly connected. The qualified samples are sent to the customer for confirmation. The customer evaluates the samples according to their actual needs and provides suggestions for improvement. After receiving the customer’s feedback, the design and sampling process is adjusted and optimized in a timely manner until the customer is completely satisfied with the samples. Both parties confirm the final sampling plan, which provides an accurate basis for formal production.
In the production of plastic hinge jewelry boxes, common plastic materials include PET (polyethylene terephthalate), PVC (polyvinyl chloride), PP (polypropylene), etc., each with their own characteristics and applicable scenarios.
The Richpack factory Richline always adheres to strict quality and environmental protection requirements, and uses plastic pellets like PP materials with GRS certification. This material has high heat resistance, can maintain stability to a certain extent in high temperature environments, is not easily deformed, and is suitable for use in jewelry boxes that need to be stored or transported in high temperature environments . It also has good chemical resistance and can withstand the erosion of some common chemicals.
PP material has a low density and is lightweight, which can reduce the overall weight of the plastic box, making it easy to carry and transport. It is often used in the production of plastic boxes for daily wear jewelry. When selecting plastic materials, it is necessary to comprehensively consider factors such as the positioning of the jewelry box, cost budget, environmental protection requirements, and product characteristics to ensure that the selected materials can meet the various performance requirements of the product.
In order to achieve the best appearance and performance of the plastic hinge jewelry box, the choice of paper materials needs to match the plastic materials. In terms of material, common types of paper include white cardboard, coated paper, and specialty paper. White cardboard has high stiffness and can provide good structural support for the plastic box, making it more durable. Its smooth surface and good printability can present clear and exquisite printed patterns. It is suitable for use with plastic materials with high transparency, such as PET, to make high-end jewelry boxes that show a simple and elegant texture.
Art paper liike pearlescent paper and laser card has high gloss and good ink absorbency. The printed patterns have bright colors and rich layers, which can enhance the visual appeal of the box. Special papers such as pearl paper and patterned paper have unique textures and feel, which can add a unique artistic atmosphere to the box, enhance the product’s grade and added value, and are often used in high-end custom jewelry boxes.
Combined with high-quality plastic materials, they create a one-of-a-kind packaging effect. The color and texture should be chosen according to the style and brand image of the jewelry. For simple style jewelry, plain-colored paper with simple textures can be selected to highlight the simple beauty of the jewelry; for retro style jewelry, paper with retro textures or colors can be selected to create a strong retro atmosphere. By carefully matching paper and plastic materials, the appearance and performance of the plastic box can be perfectly unified to meet the dual needs of consumers for aesthetics and quality.
Injection molding is a key process in plastic hinge jewelry box production. The basic principle is to add granular plastic raw materials to the cylinder of the injection molding machine. The cylinder is heated to a molten state by an external heating device, such as an electric heating coil, so that the plastic raw materials have good fluidity. Driven by the rotation of the screw, the molten plastic raw materials are compressed and conveyed forward, and injected at high speed through the nozzle of the injection molding machine into the closed mold cavity. The shape of the mold cavity is the same as the final shape of the plastic box. The plastic raw material quickly fills the cavity and fills every corner, forming the prototype of the plastic box. Then, the mold maintains a certain pressure and temperature, so that the plastic raw material continues to cool and solidify in the cavity. During the cooling process, the plastic raw material gradually loses its liquidity and the shape is fixed, finally forming a plastic box product with a certain strength and dimensional accuracy.
Once the plastic case has completely cooled and solidified, the mold is opened and the ejector mechanism is used to push the molded plastic case out of the mold, completing the injection molding process. During the injection molding process, the control of parameters such as temperature, pressure and time is crucial and directly affects the quality and performance of the plastic case. For example, too high a temperature may cause the plastic raw material to decompose and burn, affecting the appearance and performance of the plastic case; too low a temperature may make the plastic raw material less fluid, preventing it from filling the mold cavity, resulting in a product with insufficient material. Excessive pressure may cause defects such as flash and deformation in the plastic box; too little pressure may result in insufficient density and strength of the plastic box. Improper timing control will also affect the quality of the plastic box. A short cooling time may cause the plastic box to deform after demoulding, while an excessively long cooling time will reduce production efficiency. Therefore, during the injection moulding process, these parameters need to be precisely controlled according to the characteristics of the plastic material and the design requirements of the plastic box to ensure the production of high-quality plastic box products.
The mold is a key tool in injection molding, and its design and production quality directly affects the injection molding quality and production efficiency of the plastic box. In terms of mold design, the first step is to use professional mold design software, such as UG and Pro/E, to perform 3D modeling of the mold based on the plastic box design drawings and dimensional requirements. During the modeling process, factors such as the structural characteristics of the box, the demolding method, and the position of the gate are fully considered to ensure that the mold design is reasonable and feasible. For example, for boxes with complex shapes, a reasonable parting surface needs to be designed to facilitate the opening and closing of the mold and the demolding of the box; for thin-walled boxes, the position and size of the gate should be optimized to ensure that the plastic material can quickly and evenly fill the cavity, avoiding underfilling or overfilling.
At the same time, the cooling system design of the mold should be considered, and the cooling channels should be arranged reasonably to ensure that the mold can be evenly cooled during the injection molding process, shorten the cooling time, and improve production efficiency. During the mold making process, high-quality mold steels such as P20, 718, and NAK80 are selected. According to the mold design drawings, various parts of the mold are precisely machined through a variety of processes such as machining, EDM, and wire cutting. During the processing, the processing accuracy is strictly controlled to ensure that the dimensional tolerances of the mold parts are within the allowable range. Generally, the dimensional tolerances of the mold cavities and cores are controlled within ±0.01mm to ensure the dimensional accuracy and surface quality of the plastic hinge jewelry box. After the mold is completed, it is assembled and adjusted strictly to check whether the mold opens and closes smoothly and whether the parts fit together tightly, so as to ensure that the mold can operate normally. Through careful design and production of the mold, a reliable guarantee is provided for injection molding, and high-quality plastic hinge jewelry boxes are produced.
In the production process of the plastic hinge jewelry box, the application of printing processes plays a key role in enhancing the aesthetics and brand recognition of the box. Common printing processes include UV offset printing and screen printing, each with their own characteristics and applicable scenarios. UV offset printing is a high-precision printing process that uses ultraviolet light to cure the ink.
Using the CMYK four-color printing principle, it can achieve very delicate color reproduction and high-precision pattern printing. This printing process is suitable for printing on boxes with high print quality requirements, complex patterns and rich colors. For example, for jewelry boxes that need to print delicate jewelry patterns, fine brand logos or have rich color gradient effects, UV offset printing can accurately render the details and color layers of the pattern, making the printing effect realistic and vivid, and adding a gorgeous texture to the box. Silk screen printing involves pressing a squeegee against the screen to transfer the ink through the mesh to the substrate, creating an image identical to the original. The ink layer is thick, with good coverage and a three-dimensional feel, and is suitable for printing patterns that require a prominent texture and three-dimensional feel, such as metallic patterns and frosted text. In addition, silk screen printing can also use special inks, such as fluorescent inks and luminous inks, to give the box a unique visual effect. When choosing a printing process, it is necessary to comprehensively consider factors such as the design requirements of the plastic box, the characteristics of the printed pattern, and the cost budget, in order to determine the most suitable printing process, ensure that the printing effect can meet the needs of customers, and at the same time improve the overall quality and market competitiveness of the plastic box.
In order to protect the printed pattern on the surface of the plastic hinge jewelry box and improve the durability of the box, it is usually necessary to apply an anti-scratch treatment. Applying an anti-scratch oil is a common treatment process. The main function of applying an anti-scratch oil is to form a hard, wear-resistant protective film on the surface of the box, which effectively prevents the box from being scratched or worn during daily use and transportation, thereby maintaining the surface finish and the integrity of the printed pattern. During the operation, first ensure that the surface of the plastic box is clean, dry, and free of dust, oil, and other impurities, so as not to affect the adhesion of the scratch-resistant oil. Then, according to the type and characteristics of the scratch-resistant oil, choose an appropriate coating method. Common coating methods include spraying, rolling, and showering. Spraying can evenly distribute the scratch-resistant oil on the surface of the box, forming a relatively even coating thickness, and is suitable for boxes with high coating quality requirements. Rolling is simple to operate and highly efficient, and is suitable for coating large areas of the box surface. Dipping is suitable for boxes with regular shapes that are mass-produced, and can quickly and efficiently complete the coating operation. During the coating process, the thickness of the scratch-resistant oil coating must be strictly controlled. Generally, a coating thickness of 3-5μm is appropriate. A coating thickness that is too thin may not achieve a good scratch-resistant effect, while a coating thickness that is too thick may cause defects such as flow marks and bubbles on the surface of the box, affecting the appearance quality of the box. After the coating is complete, place the box in a drying device and carry out appropriate drying and curing treatment according to the curing conditions of the scratch-resistant oil to form a firm protective film on the surface of the box. Treating the box with scratch-resistant oil can effectively improve the scratch resistance of the box, extend its service life, and at the same time maintain the aesthetics and value of the product.
Paper laminating is the process of pasting the cut paper on the surface of the injection molded carton, and its operation process and glue use have an important impact on the quality and appearance of the carton. Before laminating, the glue box and paper should be pre-treated to ensure that the surface of the glue box is clean, dry and free of oil, dust and other impurities, in order to enhance the adhesion of the glue; the surface of the paper should also be flat, no wrinkles, and the paper can be flattened if necessary. Then, choose the right glue, common paper laminating glue has white latex, hot melt glue, etc.. White latex adhesive has the advantages of high adhesive strength, moderate drying speed, environmental protection, etc., suitable for most of the paper and plastic material laminating; hot melt adhesive has a fast curing speed, adhesive strength, commonly used in the need for rapid prototyping of laminating process. In the use of glue, according to the characteristics of the glue and the requirements of paper laminating, control the amount of glue coating and coating method. Generally, roller coating, spraying and other ways of glue coating can be used to ensure that the glue is evenly distributed on the surface of the glue box or the back of the paper. The amount of coating should be moderate, too much coating will lead to glue overflow, affecting the appearance of the box, but also may cause uneven bonding between the paper and the box; too little coating will lead to bonding is not strong, the paper is easy to fall off. Next, the paper is accurately laminated to the surface of the box, using pressing equipment or hand tools for pressing, so that the paper and the box are tightly combined to eliminate air bubbles in the middle. During the lamination process, care should be taken to keep the paper flat and accurately positioned to avoid problems such as paper offset and folds. After the lamination is completed, the glue box will be placed in a well-ventilated, suitable temperature environment for drying, so that the glue is fully cured. In the drying process, to avoid extrusion or collision of the glue box by external forces, so as not to affect the quality and effect of laminating. Through strict control of the laminating process operation, ensure that the paper and the glue box are firmly bonded, the appearance is flat and beautiful, and improve the overall quality of the glue box.
Die-cutting is the process of cutting the carton after laminating according to the designed shape and size, and its precision directly affects the molding quality of the carton. Before die-cutting, a high-precision die-cutting plate should be made according to the design drawings of the carton. The design of the die-cutting knife plate should be completely consistent with the shape and size of the box, and the lines of the knife plate should be smooth and accurate to avoid burrs, deviations and other problems. At the same time, to choose a reliable quality of die-cutting knife, the sharpness and durability of the knife directly affect the effect and efficiency of the die-cutting. In the die-cutting operation, the laminating carton is placed on the die-cutting machine, adjust the parameters of the die-cutting machine, such as pressure, speed, etc., to ensure that the die-cutting process is stable and accurate. Too much pressure may lead to rupture and deformation of the box, too little pressure will make the die-cutting incomplete; too fast speed may affect the accuracy of the die-cutting, too slow speed will reduce production efficiency. Generally speaking, the die-cutting pressure should be adjusted according to the material and thickness of the box, for thicker boxes, need to appropriately increase the die-cutting pressure; die-cutting speed should be controlled within a reasonable range to ensure that the quality of the die-cutting and the balance of production efficiency. Die cutting is completed, the box will be left on some excess waste, need to be cleaned up waste disposal. When clearing the waste, be careful to avoid damage to the edges and surfaces of the box, to ensure the integrity and aesthetics of the box. You can use manual or mechanical way of waste removal, manual waste removal is suitable for small batch production or high precision requirements for waste removal, can be more detailed removal of waste; mechanical waste removal is suitable for mass production, high efficiency, but need to pay attention to the adjustment and operation of the equipment to ensure that the effect of waste removal. Through strict control of die-cutting and waste removal, it ensures that the shape and size of the carton are accurate, providing a good foundation for subsequent assembly and use.
Bonding and bottoming is an important part of plastic hinge jewelry box molding and assembly, which directly affects the structural stability and function of the box. In the gluing process, for the parts that need to be glued, such as the side of the box, flap, etc., the appropriate amount of glue should be applied first. The choice of glue should be made according to the material of the glue box and the use environment to ensure that the glue has good adhesive strength and durability. When applying glue, it should be even and appropriate amount to avoid the situation that too much glue overflows and contaminates the surface of the box, or too little glue leads to weak bonding.
After applying the glue, align the parts to be bonded accurately, use jigs or manual pressure to fix, so that the glue gives full play to the bonding effect, and wait for the glue to cure.
In the scale production system of plastic hinge jewelry box, the automatic box wrapping machine, as the key hub of intelligent manufacturing, relies on the Industry 4.0 technology architecture to realize the two-dimensional leap in production efficiency and product quality, and builds up a modern and intelligent production paradigm.
In the material loading process, the automatic cartoning machine integrates an automated loading system based on machine vision recognition and six-axis robotic arm coordination. The system captures real-time images of molded carton parts with the help of high-resolution CCD cameras, and through advanced image recognition algorithms, it can accurately identify the position, attitude and model information of the parts within milliseconds. Based on the recognition results, the six-axis robotic arm realizes accurate gripping and positioning of the parts with a gripping accuracy of ±0.1mm by virtue of its flexible movement characteristics of multiple degrees of freedom, ensuring that the parts enter the subsequent process with zero deviation.
Entering the gluing process, the automatic carton wrapping machine is equipped with a high-precision gluing system based on closed-loop control. The system monitors the real-time flow, pressure and temperature of the glue through pressure sensors, flow sensors and temperature sensors. Based on the monitoring data, the PID control algorithm is used to accurately regulate the drive motor, pressure pump and other actuators of the gluing equipment to ensure that the control accuracy of the gluing volume reaches ±0.01g and the fluctuation range of the gluing speed is controlled at ±1mm/s under the conditions of different glue characteristics (e.g., viscosity, curing speed) and box materials (e.g., PP, PS, ABS, etc.) to achieve uniform and stable glue application and provide high quality adhesion. The glue is evenly and stably applied, providing a reliable guarantee for high-quality bonding.
Folding and assembling process is the core process of automatic carton wrapping machine, which adopts the cooperative operation mode of multi-axis linkage robotic arm and high-precision mold. The multi-axis linkage robot arm has high-speed, high-precision motion performance, with a repeatable positioning accuracy of ±0.05mm, and can fold and assemble the carton parts in precise order and angle according to the preset three-dimensional motion trajectory. Meanwhile, with the high-precision positioning system based on laser distance measurement and capacitive displacement sensor, and the pressure control system with adaptive control function, the relative position and pressure changes between components are monitored in real time during the assembly process to ensure that the components are connected tightly, and the dimensional accuracy is controlled within ±0.2mm, which can satisfy the requirements of high-precision assembly.
In the finished product output stage, the assembled boxes first enter the quality inspection system based on machine vision and artificial intelligence algorithms. The system carries out all-round inspection on the appearance, size and adhesive quality of the box through multi-view high-definition cameras, and analyzes and processes the collected image data with deep learning algorithms, which can quickly and accurately identify all kinds of quality defects, such as glue overflow, misalignment of parts, surface defects, and so on. Qualified boxes are automatically transported to the next packaging process by the automated conveyor in accordance with the set beats and paths, realizing the seamless integration of the production process.
The automatic jewelry box wrapping machine is equipped with a distributed control system based on industrial Ethernet, with high-performance PLC as the core control unit, realizing real-time and precise control of each actuator of the equipment. The system has strong computing and data processing capabilities, and can complete the collection, analysis and processing of various types of sensor data in microseconds, and according to the preset production process parameters, automatically adjust the amount of glue, folding angle, pressure and other key process parameters to ensure the efficient and stable operation of the production process. At the same time, through the seamless connection with enterprise MES system, real-time uploading and sharing of production data can be realized, which provides powerful data support for enterprise’s production management and decision-making. Richpack automatic carton wrapping machine also adopts high-strength alloy steel as the main structural material, and is optimized and designed by finite element analysis, which ensures the structural stability of the equipment in high-speed and heavy-duty operation conditions. The key moving parts, such as arm joints, guide rails, screws, etc., adopt high-precision ball screws, linear guide rails and servo motors, which, together with advanced lubrication and sealing technology, can effectively reduce the wear and energy consumption of the equipment, and improve the operating efficiency and service life of the equipment.
The automatic box wrapping machine shows significant technical advantages in plastic hinge jewelry box production. In terms of production efficiency, its maximum capacity can reach 1000 – 1500 plastic boxes per hour, compared with the traditional manual box wrapping method, the efficiency increased by 5 – 8 times, to fully meet the needs of large-scale, high-efficiency production. In terms of product quality control, with the high-precision automated assembly and inspection system, the passing rate of the products can reach over 98%, which effectively reduces the rate of defective products caused by manual errors. From the cost control point of view, the application of automatic carton wrapping machine significantly reduces the labor input, and at the same time, through accurate process control, improves the utilization of raw materials and reduces the production cost. In addition, the equipment has a high degree of flexibility and expandability, through the software programming and parameter adjustment, can quickly adapt to different box design and production requirements, for the enterprise’s product innovation and market expansion to provide strong support.
Installation of hinge is a key step that affects the opening and closing convenience and service life of plastic hinge jewelry box. According to the design of the jewelry box, the hinge type and specification should be selected reasonably. Ordinary hinges are suitable for regular jewelry boxes to realize the basic opening and closing function; spring hinges with automatic closing characteristics are commonly used in jewelry boxes with higher requirements for opening and closing convenience.
When installing the hinge, Richpack workers first utilize the automated punching equipment to accurately locate and control the holes in the corresponding position of the box to ensure accurate installation of the hinge. Subsequently, use screws or glue to firmly fix one end of the hinge on one side of the rubber box to prevent loosening. After the installation is completed, the hinge is carefully debugged to check the smoothness of the glue box opening and closing and the flexibility of the hinge rotation, and adjust the abnormal situation in time.
The purpose of bubble compaction is to ensure that the internal structure of the box is tight and free of bubbles and voids after assembly, so as to enhance the overall strength and stability. For boxes bonded with hot melt adhesive, a hot press is used for bubble compaction. By precisely controlling the temperature, pressure and time, the hot press can make the glue re-melt under the appropriate temperature, fill the air bubbles and enhance the adhesive strength, and at the same time, avoid the deformation of the box caused by improper temperature and pressure.
For the use of other glues or boxes that do not need to be heated, the cold press is utilized to apply pressure to squeeze out the internal air bubbles to make the parts fit tightly. After the pressure bubble compaction is completed, check the box comprehensively to ensure that the interior is tight and the surface is flat.
After the assembly of the box is completed, the cleaning process is an important part to ensure the appearance quality. Because the surface of the box is easily contaminated with dust, oil and other impurities during the production process, which affects the appearance and quality. Use a soft dust-free cloth or sponge, dipped in the appropriate amount of detergent, gently wipe the surface of the box, control the wiping strength, to prevent scratches. For stubborn stains, use a special cleaner to ensure that the material of the box is not damaged.
After wiping, dry the surface with a clean, dust-free cloth to remove the residue of cleaner and moisture. At the same time, the use of vacuuming equipment to clean up the dust impurities inside the box to ensure internal cleanliness. Finally, the cleaned box is labled and packaged to enter the subsequent stages.
After the carton is cleaned and packaged, it will enter the quality sampling process. According to the established sampling ratio, a certain number of boxes are randomly selected from each batch. The inspection not only includes a second verification of the appearance, to ensure that there is no leakage of rubbing stains, no scratches added; but also to reconfirm the dimensional accuracy, the use of high-precision measuring instruments, such as the coordinate measuring machine, to detect the length, width and height of the box, the hinge holes and other key dimensions of the hinge, the permissible error is controlled in a very small range, to ensure that the product is fully consistent with the design drawings. For the opening and closing performance of the hinge, simulated opening and closing tests are conducted, and the number of tests is set according to the product standards to ensure that the hinge remains smooth in long-term use, with no snagging and loosening phenomenon. For the hot and cold pressing treatment of the glue box, sampling destructive test, check the firmness of the internal structure, to determine whether the adhesive strength of the glue is up to standard. Once found unqualified products, immediately trace back the production link, investigate the root cause of the problem, take corrective measures to ensure the consistency of the product quality of the whole batch.
The boxes that pass the quality sampling test enter the packaging and storage process. According to the size, shape and quantity of the carton, choose the appropriate outer packaging materials, such as corrugated cardboard boxes, plastic crates, etc..
During the packaging process, buffer materials, such as foam board, bubble wrap, etc., are used to protect the cartons from damage caused by collision and extrusion during transportation and storage. Each outer package should be clearly labeled with product name, specifications, quantity, production date, batch number and other information to facilitate product identification and traceability. Packaging completed products in accordance with the category, batch neatly stacked in the designated area of the warehouse, follow the principle of first-in-first-out management. The warehouse should be kept dry and ventilated, and the temperature and humidity should be well controlled to avoid the environmental factors affecting the quality of the carton. At the same time, the establishment of a perfect inventory management system, real-time monitoring of inventory quantities, for production planning and sales delivery to provide accurate data support.
The size of the top cover of the box is slightly larger than the bottom cover, the difference between the length and width is 3-5mm, the difference between the height is 5-10mm; the outer shell of the book-type box is longer than the inner box by 5-8mm, wider than the inner box by 3-5mm; the gap between the inner box and the outer box of the drawer box is 1-2mm on one side.
Design reinforcement or reinforcement structure at the edges and corners of paper boxes, such as adding cardboard at the edges of sky and earth boxes, and using reinforcement patches at the corners of book-type boxes; ensure that the folding lines are clear and the glue at the connection parts is evenly coated; and increase the support structure for large-size or heavy-loaded jewelry paper boxes, taking into consideration of the distribution of the weight of the jewelry and the position of the center of gravity.
Paper weight 250 – 400g/m², good flatness, whiteness above 85% and uniform; gray board thickness 1 – 3mm, high hardness, in line with environmental standards, using recyclable and non-polluting raw materials.
The color accuracy is calibrated by Pantone color card, major color error ΔE ≤ 3, minor color ΔE ≤ 5; pattern edges are clear and no ghosting, plate making with high resolution images and advanced technology, control pressure and ink transfer volume during printing.
Injection temperature depends on the material, such as PET barrel front section 250 – 280℃, middle section 260 – 290℃, rear section 240 – 260℃; injection pressure 50 – 120MPa, holding pressure is 30% – 60% of the injection pressure; injection time 3 – 10 seconds, holding time 5 – 15 seconds, cooling time 10 – 30 seconds.
Mold cavity and core size tolerance ±0.05mm or less, surface roughness Ra 0.8μm or less, the parting surface is flat and close; use high quality mold steel, regular cleaning, inspection, maintenance and lubrication.
Accurate printing color, main color color difference ΔE ≤ 3, secondary color ΔE ≤ 5, clear patterns without ghosting; anti-scratch treatment is wear-resistant, no defects in appearance, and the anti-scratch layer is even and firm.
High-end hinge jewelry box can choose 350 – 450g/m² white cardboard or special paper, middle and low-end can choose 250 – 350g/m² coated paper or ordinary white cardboard; paper needs to be pre-treated to ensure that the surface is flat and free of impurities.
Paper boxes test the appearance, size, structural strength; Plastic boxes test the appearance, size, performance (compression, impact resistance, scratch resistance, etc.), size deviation is generally controlled within ± 0.5mm.
paper boxes printing color deviation, pattern blurring can change the ink and equipment, strengthen the color management; surface finishing errors can be trained operators, optimize process parameters; die-cutting assembly problems can be updated equipment, standardize the use of glue. Plastic box injection molding process errors can be adjusted parameters, training personnel, maintenance of equipment; printing faults can be repaired and debugging equipment; external laminating paper problems can optimize the cutting process, choose the right glue.
This blog comprehensively analyzes the whole production process and production specifications of paper jewelry box and plastic hinge jewelry box. In terms of the production process, paper jewelry box production through the pre-preparation, printing, surface finishing, die-cutting and slotting, laminating and assembling, as well as quality inspection and packaging, etc., each link has its own unique operating points and technical requirements. Plastic hinge jewelry box production from the receipt of the order and sampling, through the procurement and processing of raw materials, injection molding, surface printing and processing, laminating paper processing, as well as molding and production specifications. The production of plastic hinge jewelry box starts from order receiving and sampling, and goes through raw material purchasing and processing, injection molding, surface printing and processing, paper laminating, and molding and assembling, etc., and finally completes the production of the product, which is closely connected with each other, and has strict requirements for craftsmanship and quality control.
In the production specifications, paper jewelry box production in the structural design, material use, printing quality, surface finishing and assembly and inspection, etc. have formulated a detailed specification standards to ensure that the structural strength of the paper box, the appearance of the quality and performance. plastic hinge jewelry box production in the injection molding, surface treatment, paper laminating, molding and assembly, and quality inspection, etc. also have a detailed specification standards. Plastic hinge jewelry box production in the injection molding, surface treatment, external laminating paper, molding and assembly, as well as quality testing and other aspects of the specifications are also clear, covering the process parameters, quality standards, material selection and other aspects, to protect the quality and stability of the plastic box. Through the analysis of successful and problematic cases, the importance of following the production process and specifications is further verified, as well as the quality problems and solutions that may be brought about by non-standard operation. If you are engaged in the jewelry industry, or have the need to customize high-quality jewelry boxes, why not work together with Richpack jewelry packaging solutions, we create a high-quality jewelry box that meets your needs. Contact us for the journey of excellence in jewelry packaging.
Packaging sustainability development has become an unavoidable trend in the jewelry box production process, and Richpack has always integrated the concept of environmental protection into every aspect of production, and actively responded to the market’s urgent need for environmentally friendly products. In terms of material selection, we vigorously promote the use of biodegradable, recyclable and environmentally friendly materials. We will also continue to optimize the production process to reduce energy consumption and waste emissions, and guard our beautiful home for future generations. Meanwhile, intelligence and automation are becoming a strong engine for the development of the industry.
In the future, intelligent equipment and automated production lines will dominate the production of Richpack jewelry boxes. Through the introduction of advanced sensors, robots and automation control systems, every link in the production process can be precisely controlled, which greatly improves the production efficiency and shortens the production cycle, providing customers with better and more efficient services. In the future, China custom jewelry box supplier Richpack will continue to uphold the concept of sustainable development, embrace technological change, follow the market aesthetic trends, constantly innovate and optimize the jewelry box production process, create more high-quality, personalized, environmentally friendly packaging products for the jewelry industry, and work together with customers to move towards a brighter future.
Many jewelry companies are often stuck in the quagmire of choice when looking for high-quality packaging manufacturers and suppliers. Either they are overwhelmed by the dazzling array of suppliers and find it difficult to identify their reliability and professionalism; or they repeatedly hit a wall in the pursuit of unique packaging design, environmentally friendly material… Continue reading 2025 Latest Jewelry Box Manufacturing Guide: Step-by-Step & Expert Techniques
Italian jewellery packaging is an enigma, a silent yet potent storyteller. What lies beneath its alluring facade? How does it transform a simple container into a work of art that not only safeguards the precious gems within but also elevates their aesthetic appeal? Let us embark on this journey of discovery to unearth the craftsmanship… Continue reading 2025 Latest Jewelry Box Manufacturing Guide: Step-by-Step & Expert Techniques
In today’s competitive market, first impressions are paramount. Studies indicate that 72% of consumers acknowledge that packaging design significantly sways their purchasing decisions. This is particularly true in the luxury market, where perception is reality. Luxury packaging, therefore, is much more than just a container; it is an essential element of the brand experience, meticulously… Continue reading 2025 Latest Jewelry Box Manufacturing Guide: Step-by-Step & Expert Techniques
Distinctive Monogrammed Pouches for Adding a Personal Touch | Initial-Embossed Pouch Design
Jewelry Pouch with Drawstring | Stylish and Secure Storage by Richpack
Richapck Bespoke Elegant Silk Jewelry Pouches with Custom Embroidery | Tailored Packaging Solutions for Jewelry Retailers Requiring Personalized Finishing
Bespoke Handcrafted Wooden Jewelry Trays with Custom Engravings | Tailored Display Solutions for Suppliers and Retail Businesses Needing Custom Manufacturing
View MoreCustom-Printed Fabric Pouches for Branding | Tailored Packaging Solutions for Jewelry Merchants Needing Unique and Branded Presentation
View MoreCustom Zipper Pouches for Jewelry Packaging | Eco-Friendly Solutions with Personalized Designs
View MoreJust submit your email to get exclusive offers (reply within 12 hours)